Metallographic polishing, just like metallographic grinding, is the final stage in the sample preparation process of metals for subsequent analysis. Its purpose is to rectify the deformations caused by previous work steps (during sectioning and cutting). The following introduction provides some general considerations as well hints for sample preparation processes.
Metallographic polishing consists of several steps, with each step using a finer abrasive than the previous one. Tyically, a destinction between three operations is made: Pre-polishing, intermediate polishing and final polishing.
The ultimate goal is to produce a deformation-free, scratch-free, and highly reflective sample surface. For accurate results, a selection of appropriate consumables, a polishing machine, and a matching preparation guide with individual instrument settings (optimized for the according material) is required.
QATM is a leading manufacturer and supplier of high-quality consumables for polishing as well as a range of innovative metallographic polishing machines, from manual to fully automized models. The QATM application experts combine decades of experience with thousands of processed samples and will be happy to assist with your application.
|
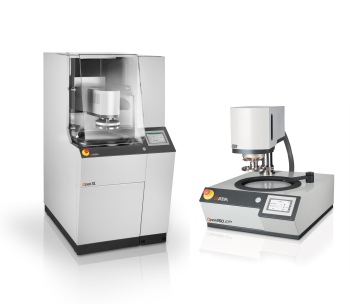
QATM offers metallographic grinders/polishers for any requirement
|
METALLOGRAPHIC POLISHING IN THREE STEPS
|
There are generally no valid rules for metallographic polishing with regard to the number and selection of polishing steps and gradation of grain sizes. However, there are preparation suggestions for the individual materials or material groups and typically a destinction between three larger process steps is made.
The range of polishing cloths covers the range of tasks for the technical material groups very well. When selecting the polishing cloth and diamond grain size, care must be taken that the pile height and the diamond grain size are selected such that the diamond grains are always in contact with the sample surface and the polishing cloth. Only then an optimal removal, and thus a good flatness/edge sharpness, are guaranteed and the metallographic polishing process is successful.
|
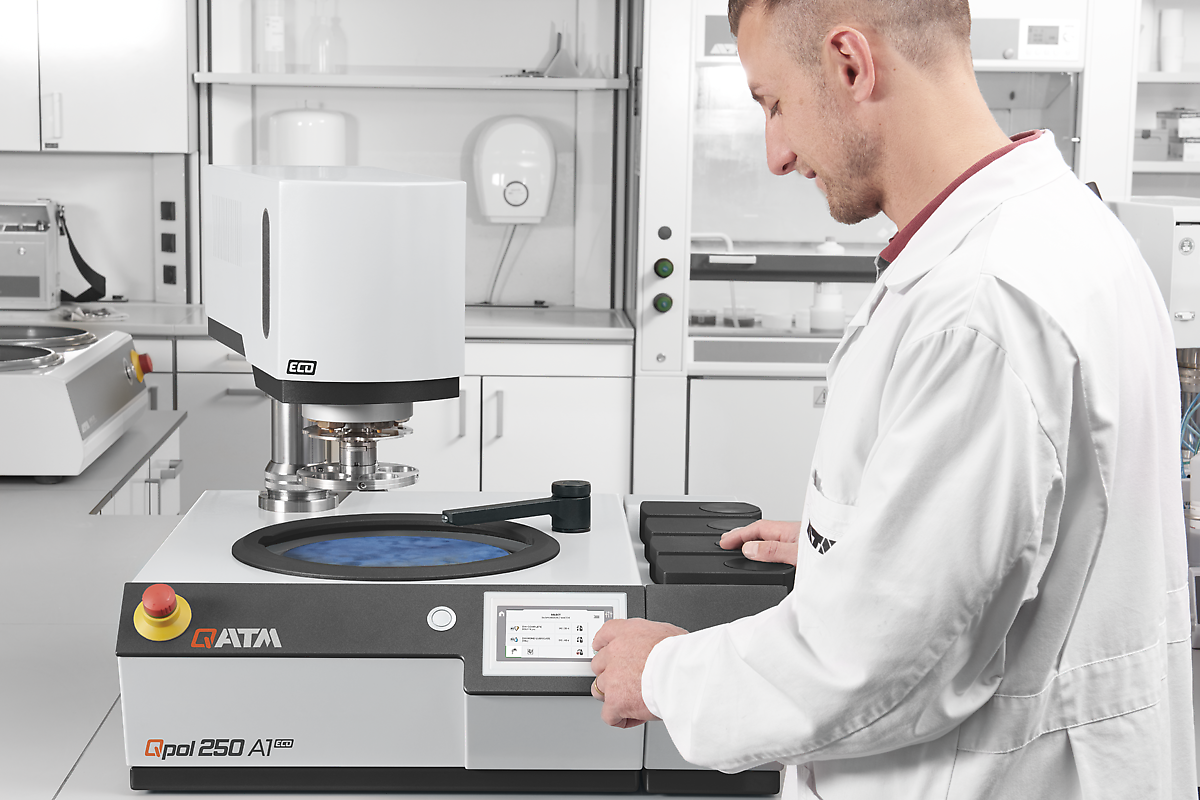
|
1. PRE-POLISHING
The general aim of metallographic pre-polishing is to achieve the best possible material removal in the shortest possible time. The good flatness of the grinding surface after the grinding process can only be maintained by ensuring that the diamond is always in motion, always rolling, if possible. This rolling motion causes the necessary removal of of excess material.
Consumables used: Diamond 15 µm to 9 µm / Hard-woven or hard-pressed cloths
2. INTERMEDIATE POLISHING
Metallographic pre-polishing is, in most cases, followed by metallographic intermediate polishing. In this step, deformation and smear layers are removed. If the material is very hard, several intermediate polishing steps may be necessary.
Consumables used: Diamond 9 µm to 3 µm / Hard-woven or lightly pile cloths
3. FINAL POLISHING
Metallographic final polishing is the last polishing step, intended to remove deformations and especially smearing on the sample surface. This step is not easy but possible. However, a final-polished finish is not necessary for every metallographic polishing task. Consumables used: Diamond 3 µm to 0.5 µm / Oxide polishing 0.1 µm to 0.06 µm / Pile or flocked cloths, foamed for oxide suspensions In metallographic final polishing, a distinction is made between purely mechanical removal by the diamond grits and chemical-mechanical removal, which is achieved by slightly alkaline final polishing suspensions. When which polishing agent is used must be determined for the individual case.
|
METALLOGRAPHIC DIAMOND POLISHING
|
In metallographic polishing, diamond polishing agents are differentiated according to the diamond shape. There are poly- and monocrystalline diamonds.
Polishing agents containing polycrystalline diamonds have clear advantages over polishing agents containing monocrystalline diamonds. The polycrystalline diamond has a uniform grain shape and many sharp edges.
The removal rate of diamond polishing agents depends on the number and size of diamond cutting edges that are working simultaneously.
For the right choice of diamond polishing or grinding abrasive (i. e. whether mono- or polycrystalline), it is important to determine its requirements beforehand. Basically, a good result can also be achieved with the cheaper monocrystalline diamond, even though the way to get there requires more effort.
Diamond polishing agents also differ in the type of their carrier material. Which of the three common carrier materials is chosen depends on the circumstances.
Diamond paste: High concentration on the polishing cloth, an additional lubricant is always necessary
Diamond suspension: Ensure well and uniform distribution on the polishing cloth, pay attention to segregation in case of a longer stationary period
Diamond spray: Ensure well and uniform distribution on the polishing cloth, an additional lubricant is always necessary, higher consumption due to dosage
|
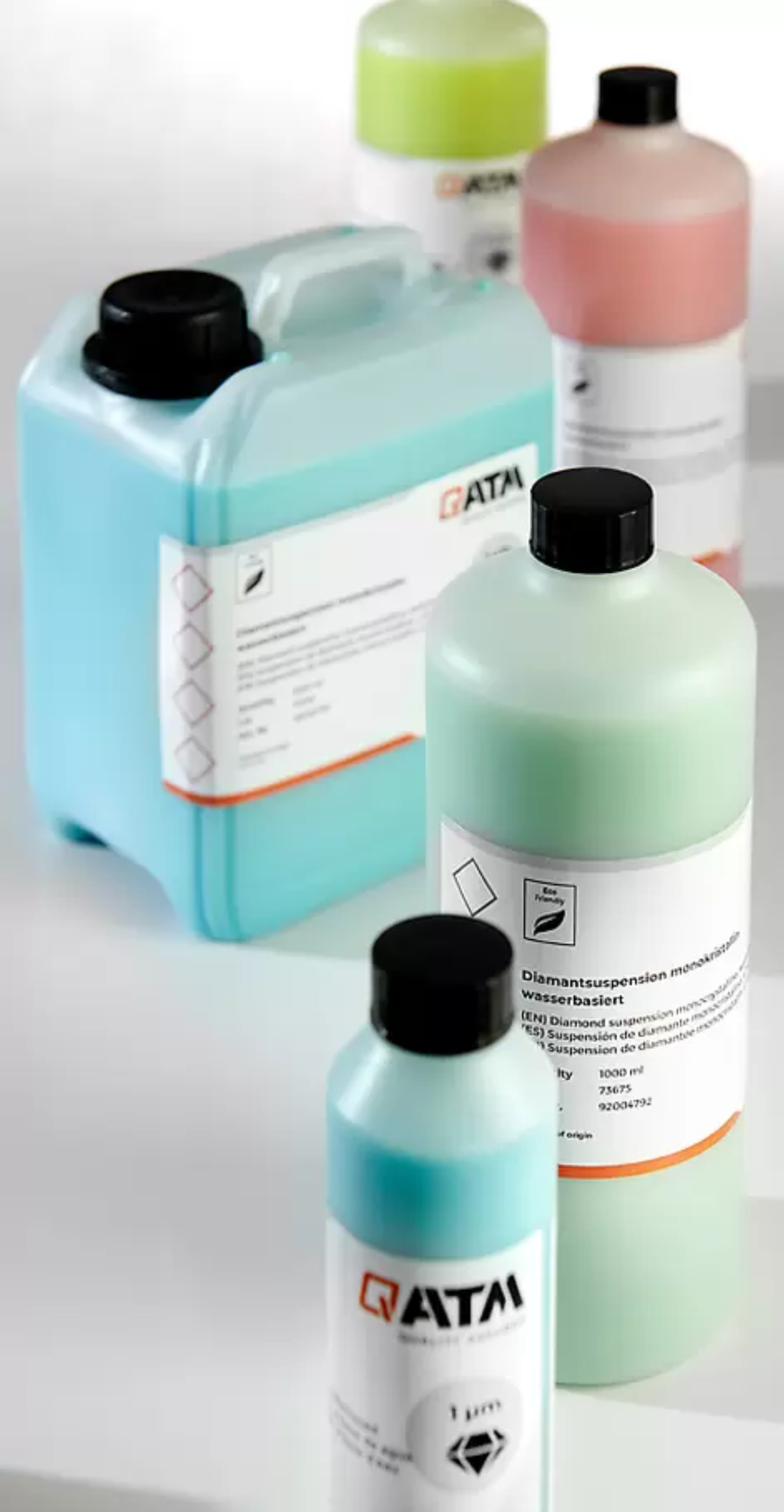
|
METALLOGRAPHIC OXIDE POLISHING
|
In metallography, oxide polishing agents are primarily used for final polishing.
A distinction is made between silicon dioxide and aluminium oxide suspensions. Both are available as "ready-to-use" aqueous or alcoholic suspension. The grain sizes are between 0.1 and 0.06 µm.
There are no absolute rules for the application of the suspensions. Alcohol-based suspensions should be used for samples which are susceptible to corrosion.
Silicon dioxide: All austenitic steels, aluminium alloys, titanium alloys, precious metal alloys
Aluminium oxide: Brass, low to unalloyed steels, grey cast iron grades
With the use of oxide polishing agents, a mechanical or chemo-mechanical removal can be achieved, which removes the smear and deformation layers that may still be present from previous metallographic polishing; the quality of this process ranges from good to very good.
The 'double' attack also results in short polishing times. Significantly lower material costs is another advantage over diamond agents
|
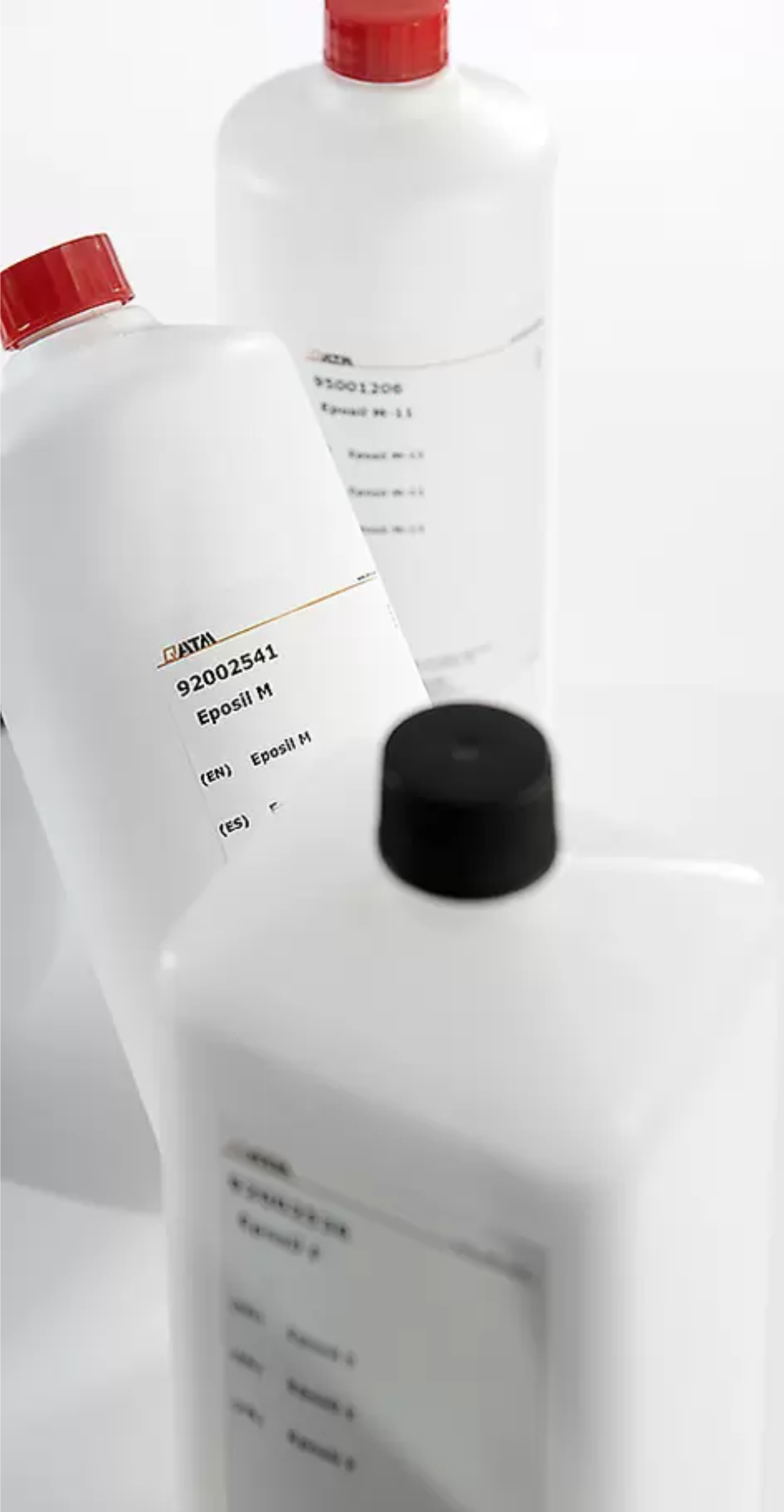
|
METALLOGRAPHIC POLISHING CLOTHS AND DISCS
|
Cloths for metallographic polishing are available with different surface structures or materials (e. g. silk, artificial silk, wool fabrics, flocked and foamed plastics). Specially developed polishing discs with integrated diamonds are also available.
Metallographic pre-polishing is usually carried out on less elastic (hard) cloths using lubricant (low impact elasticity is important to maintain edge sharpness). If edges are rounded off by cloths that are too soft, this has a negative effect on the evaluation of thin layers.
During final polishing, switch to more elastic, long-napped cloths and to lubricants with a higher viscosity.
The elasticity of the cloths for intermediate polishing lies between the two extremes just described.
|
|
|
METALLOGRAPHIC VIBRATORY POLISHING
With metallographic vibratory polishing, preparations that are nearly deformation- and scratch-free can be carried out on materials which are prone to deformation. This method is also particularly suitable for samples for EBSD analysis.
With metallographic vibratory polishing, the relative movement between a sample and polishing base necessary for removal is achieved by a vibrating work surface. The working surface is set into vertical vibrations which are superimposed by torsional vibrations. These combined vibrations cause the samples, which are weighted down with a weight, to run in a circle on the working wheel.
The metallographic vibratory polisher QPol Vibro automatically finds the best frequency for the sample movement on the polishing cloth depending on the mass to be moved. Due to the very gentle material removal, the method is particularly suitable for very soft and ductile materials such as copper or copper alloys, aluminium and aluminium alloys, Ni-based materials, as well as soft steels. However, this gentle and therefore very low material removal results in long polishing times that sometimes take considerably more than 30 minutes.
|
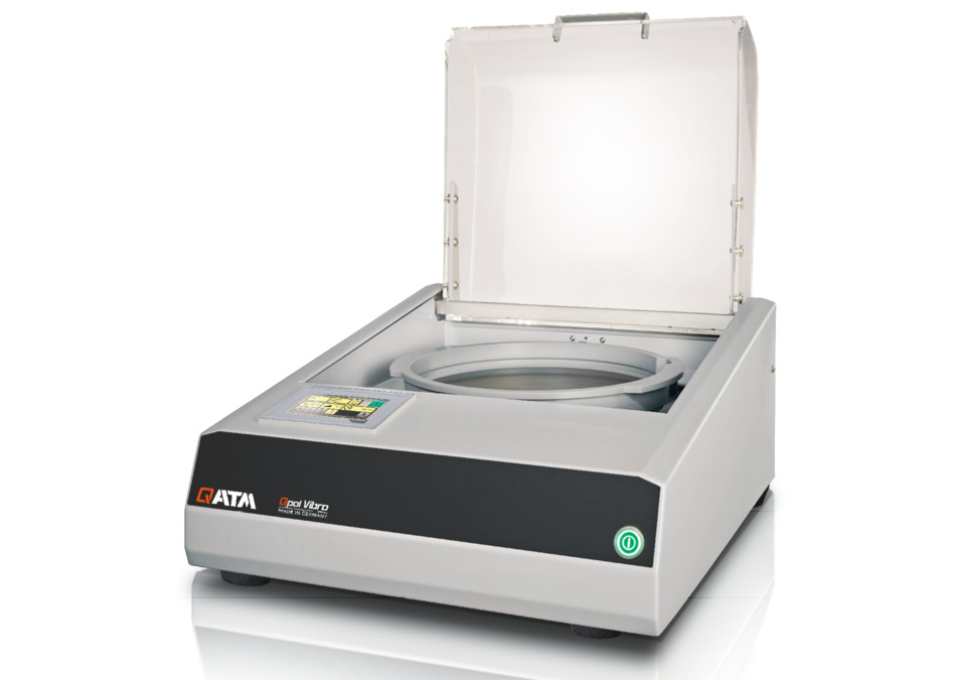
|
TIPS AND TRICKS FOR METALLOGRAPHIC GRINDING AND POLISHING
Grinding and polishing is a standard technique for metallographic sample preparation. Expert knowledge in processing is available for almost all materials. However, a number of potential sources of error must be taken into account when searching for the appropriate procedure. The procedure is very time-consuming due to the multi-stage workflows, especially in manual processing. On the other hand, larger investments must be expected if a higher degree of automation is desired.
The following risks must be evaluated in each individual case:
- The use of abrasive materials for metallographic polishing can result in scratched sample surfaces, especially if the material contains phases with different hardness values. This can never be ruled out in case of composite materials.
- Edges and grain boundaries can be rounded.
- Coolants and lubricants must not react with the material as organic materials, such as paper or fibers, would swell. If the cooling performance is not sufficient, the sample materials suffer thermal degradation and/or microstructural changes.
The market for grinding and polishing equipment is very diverse and offers suitable solutions for a large variety of applications. Depending on application and capacity, simple semi-manual to fully automatic grinding and polishing systems are available. The wide range of applications also speaks for itself. With carefully matched grinding and polishing consumables, combined with suitable preparation parameters, excellent results can be achieved for almost all materials. Mechanical grinding and polishing often is the only preparation technique suitable for ceramics, composite materials and filled/reinforced plastics.
To provide assistance to the user, a few tips and tricks for grinding and polishing are listed below.
|
1. METALLOGRAPHIC POLISHING AND GRINDING DYNAMICS
The positioning of the sample holder in relation to the working wheel is a particularly important point in semi- and fully automatic metallographic sample preparation.The positioning of the sample holder, the speed of rotation, the direction of rotation and the contact pressure are important factors for the durability of the consumables and the resulting surface quality.
If the sample holder is positioned too close to the centre, most unfavourable grinding and polishing dynamics will be the result (sketch 1).
The positioning as shown in sketch 2 is ideal for metallographic sample preparation during grinding and polishing. The sample holder should extend slightly beyond the edge of the working wheel, approximately 5 to 10 mm. Then the samples still move on the polishing cloth!
|
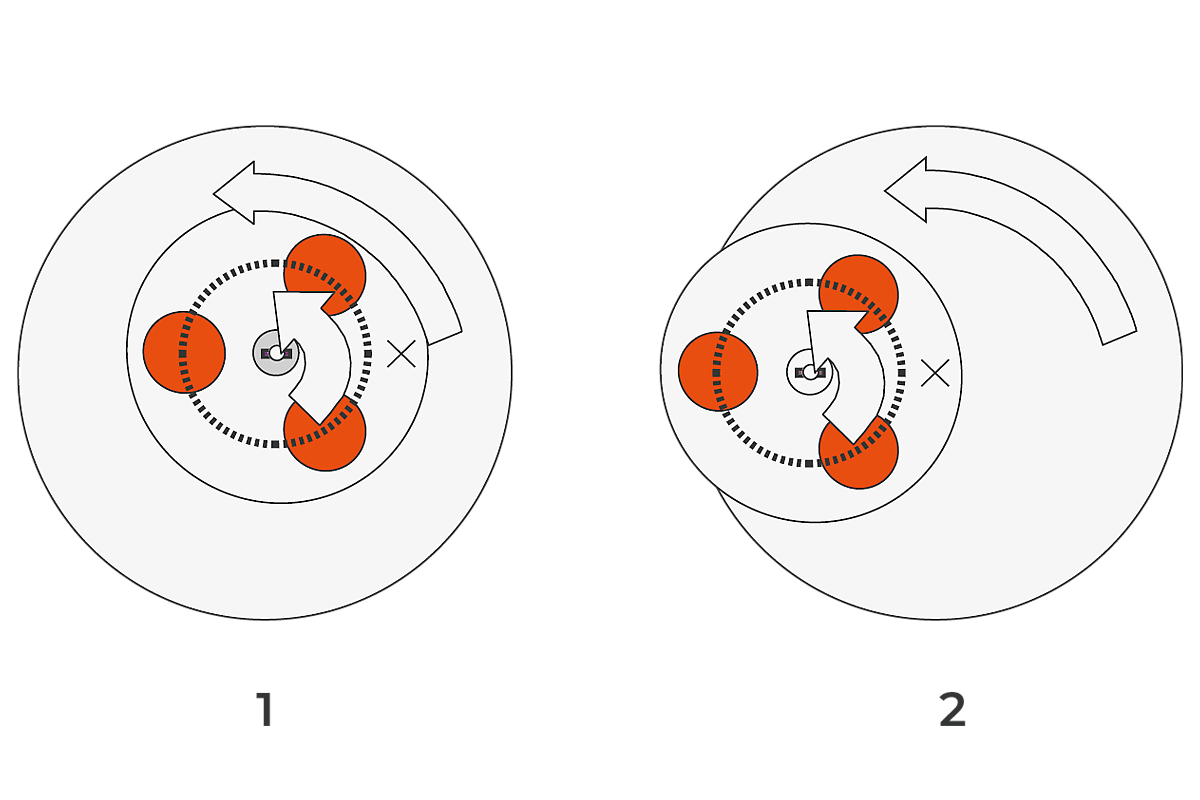
|
|
2. COMET TAILS
In metallography, the so-called comet tails usually occur with non-metallic inclusions, pores and hard phases in a soft basic matrix, if the section is only held in one grinding or polishing direction during manual preparation. This artefact is typical for large material samples. For optimum metallographic sample preparation, the samples should be moved in a way that prevents creation of a preferred direction.
|
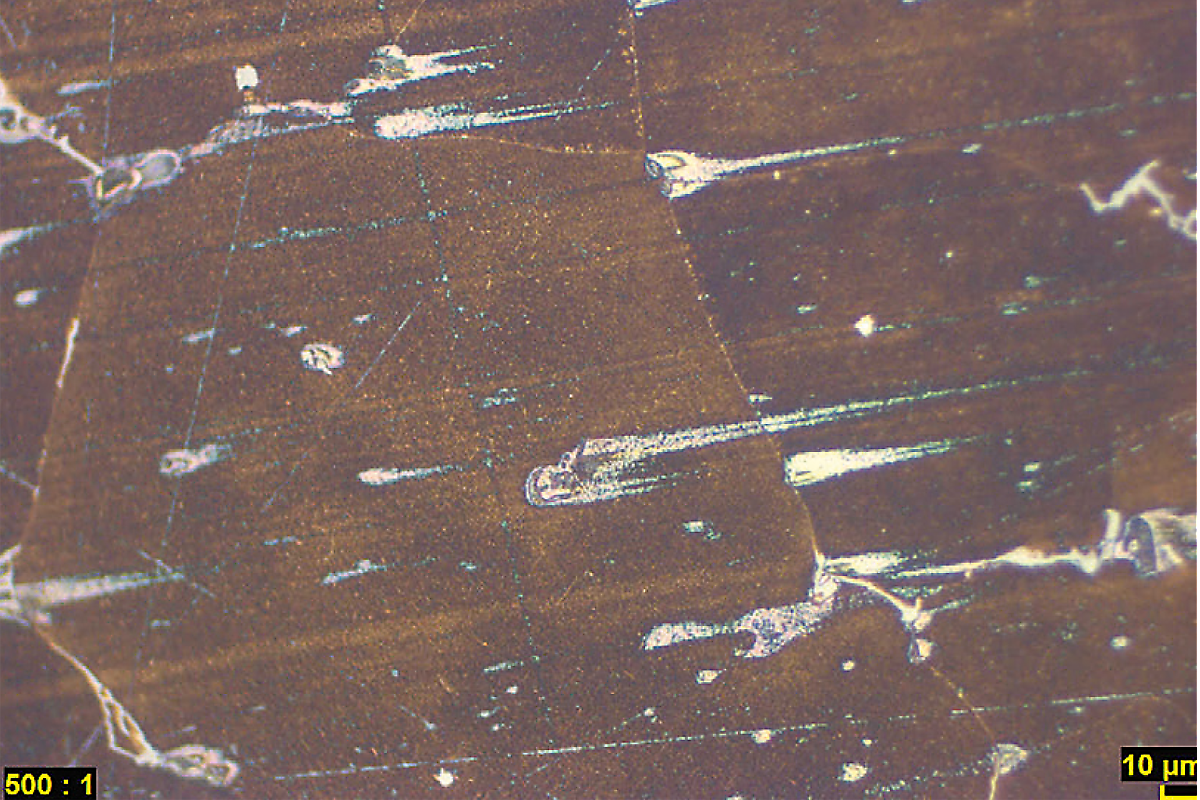
|
|
3. THE PENCIL EFFECT
In metallographic polishing, the 'pencil effect' is a widespread artefact formed during manual or single pressure preparations. The sample surface tapers towards the center which is clearly visible in the pattern on the grinding surface. This problem occurs when preparing samples with single pressure.
The causes can be:
- Sample holder with an excessively large opening, i. e. the sample has too much clearance
- Wrong diameter selected, e. g. sample diameter 38 mm (1 ½ inch) and sample holder has 40 mm
- Sample shape not adapted (too high, therefore the sample tilts back and forth)
- Contact pressure is too low, the sample starts tilting irregularly
- Non-adherence to the grinding and polishing dynamics parameters
- Sample is not cylindrical (embedding mould for cold mounting is oval)
|
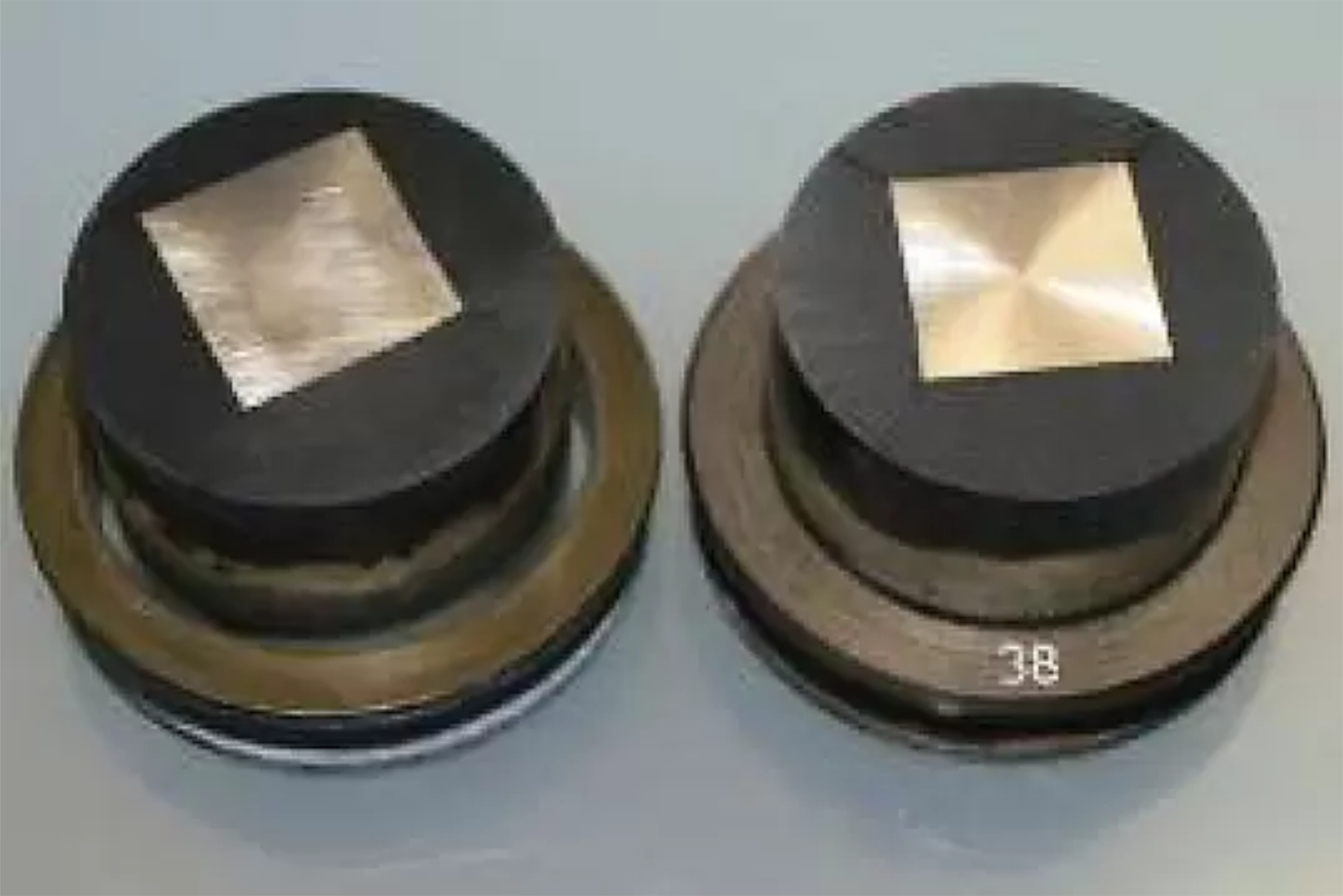
|
|
4. DEPOSITION OF METALLOGRAPHIC GRINDING AND POLISHING AGENTS
Abrasives and other polishing agents for metallography, such as silicon carbide particles from the grinding paper, diamonds from diamond polishing agents or oxides from the oxidic final polishing agents, can be pressed into the surface during metallographic sample preparation. This may occur in the following situations:
-
In case of dry metallographic grinding of composite materials consisting of very hard and very soft materials
-
In case of excessively high grinding or polishing pressure when preparing extremely soft materials and/or composite materials with components of soft and hard phases
-
In case of excessively high abrasive concentration in combination with too high pressure
-
Incorrect selection of the grain size of the grinding and polishing agent
-
When the lubricating film breaks down during polishing. If there is too little lubricant is added, the samples can heat up considerably
-
When using lubricant with very low viscosity
-
If the wrong grinding pad or polishing cloth is chosen (too hard or too soft), pay attention to impact elasticity
-
In case of too one-sided sample movement
|
|
5. METALLOGRAPHIC PREPARATION OF NITRIDED STEELS
The grinding direction can also influence the quality of the metallographic preparation result: In this manual preparation, the specimen on the left was held on the SiC paper in such a way that the grinding direction of the abrasive grain led from the steel specimen to the embedding material. The brittle nitrided layer was thus pressed into the smallest gaps of the mounting compound which resulted in breakouts.
The problem was solved by rotating the sample. It had to be ground from the mounting compound to the sample. The result (specimen on the right) has not been fully polished to make the problem and the solution clearly visible.
DIN 30902:2016-12 (Heat treatment of ferrous materials – Light microscopic determination of the thickness and porosity of the compound layer of nitrided and nitrocarburised workpieces) recommends to wrap the specimen with an aluminium or copper foil before mounting to protect the compound layer during preparation.
Here such a sample is shown in the first image on the left, on the right for comparison the unwrapped sample. Both samples were then mounted in a ground joint to ensure identical metallographic preparation (second image).
|
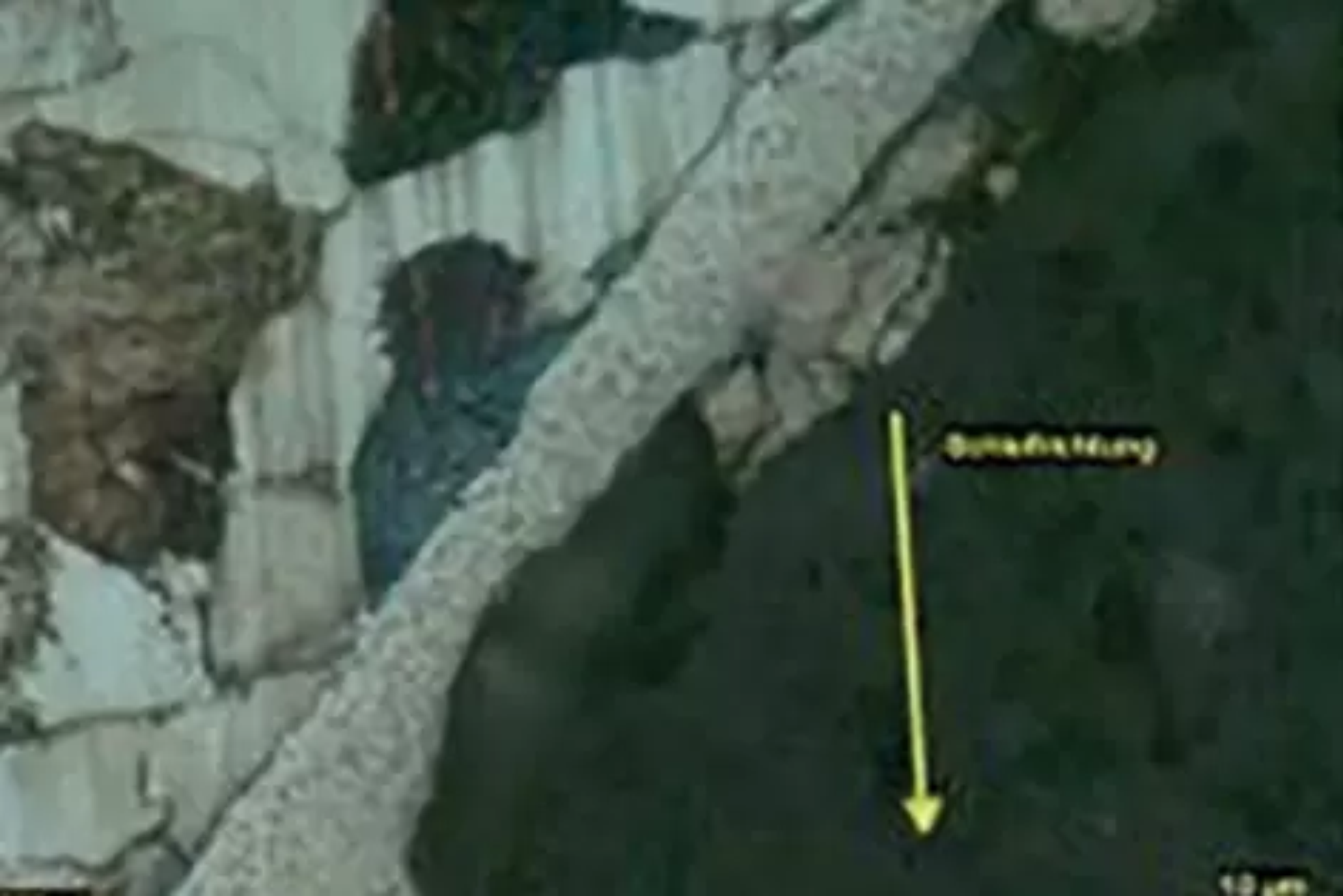
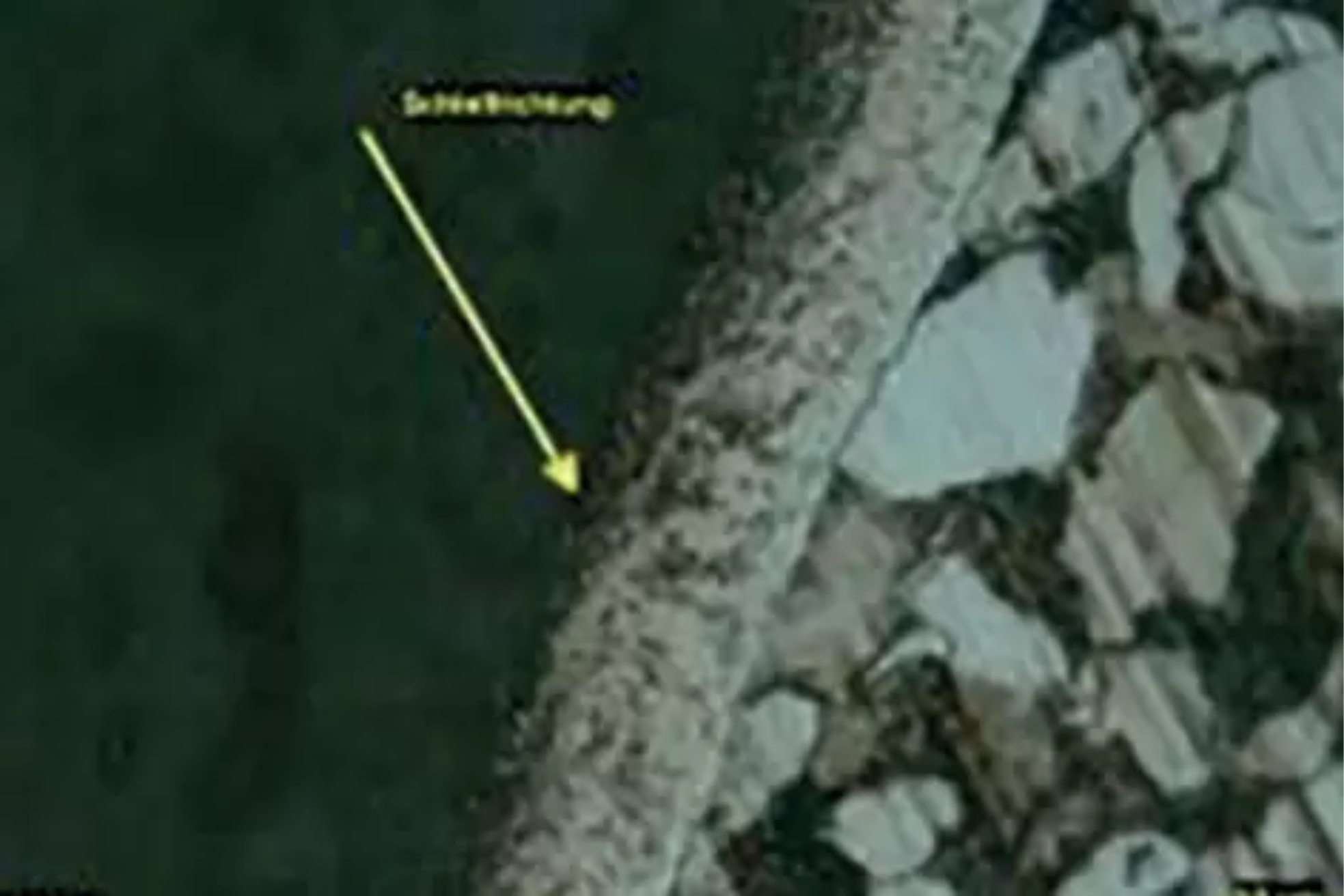
|
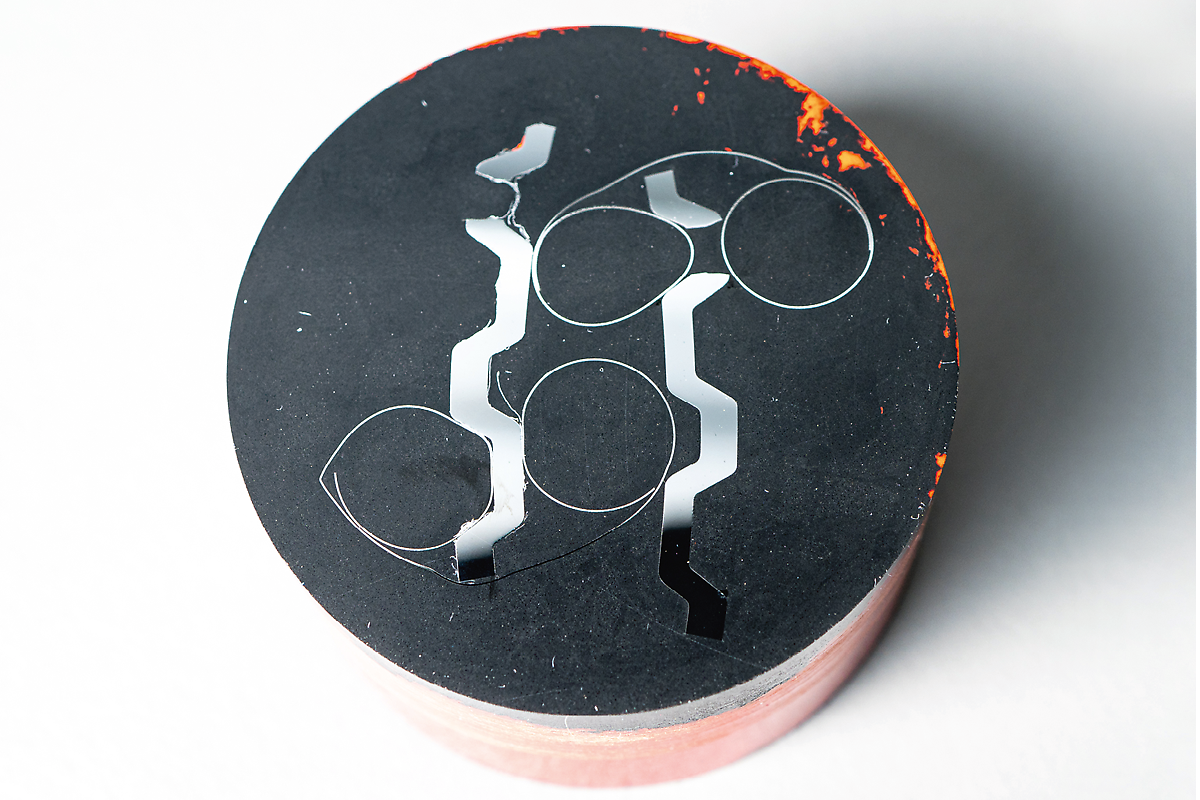
The results of the metallographic preparation show that the compound layer in the upper image is unevenly thick and shows strong chipping. On the other hand, the compound layer in the lower image is uniform and free of break-outs and can therefore be evaluated reliably. It is important to ensure that the thicker white layer above the actual bonding layer is not evaluated, this is the aluminium foil.
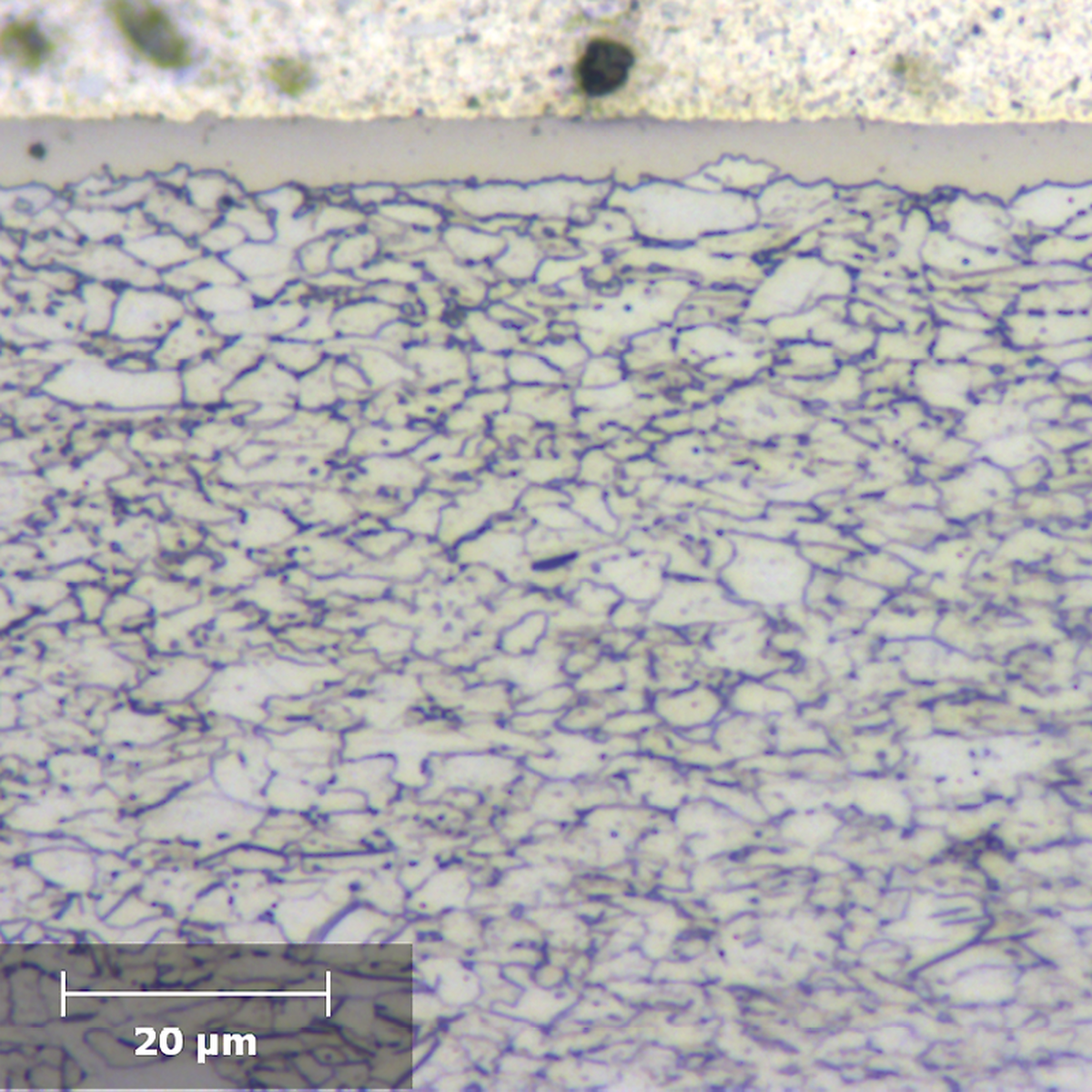
|