Metallographic cutting or sectioning usually marks the first step of the metallographic sample preparation process. In most cases it is necessary because the part or solid body is too large for the following metallographic grinding and polishing steps carried out on a laboratory scale.
Since mobile grinding and polishing machines are available in the market, there always is a possibility to prevent the sectioning process. Depending on part geometries and material hardness as well as employed analytical techniques, different cutting techniques and consumables are used.
QATM is a leading manufacturer and supplier of high-quality consumables for cutting as well as a range of innovative metallographic cut-off machines with a choice of manual or automatic axes. The QATM application experts combine decades of experience with thousands of processed samples and will be happy to assist with your application.
|
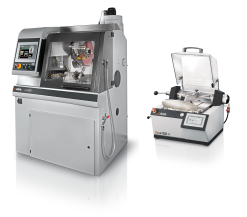
QATM offers metallographic cut-off machines for any requirement
|
SAMPLING FOR METALLOGRAPHIC ANALYSIS
|
Typical methods to sample materials for microscopic analysis are:
- Microtomy (common for polymers and very soft metals, can only be applied for thin sectioning)
- Sawing using band saws (low-cost method with low surface qualities)
- Wet Abrasive Cutting
Industry and academia commonly prefer wet abrasive cutting due to its very low impact on the material's structure, compared to other methods.
The so-called wet abrasive cutting is a machine-based cutting process. In the field of metallographic sampling, this usually means the mechanical segmentation of components to be examined.
For this purpose, cut-off wheels of different thickness, structures and bonds are used on an appropriate wet abrasive cut-off machine. Normally, they consist of a phenolic resin or rubber bond of a certain hardness and porosity in which aluminium oxide or silicon carbide grains of a certain grain size are embedded.
|
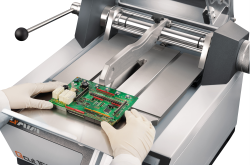 |
The following guidelines should be applied to the metallographic sectioning process:
- Cutting by wet abrasive cut-off machine with sufficient cooling and rotating disc. Otherwise, the deformation in the surface is so high that it cannot be rectified without long grinding steps.
- Optimum cooling is indispensable for evaluation. An excessively heated surface gives rise to misconceptions – artefacts simulate a false result.
- A fitting Corrosion protection agent must be added to the coolant, otherwise there is a risk of surface oxidation at the cutting surface. This is also important to protect the interior of the cutting device.
- The size and design of the cutter depend on the sample size – the main criterion is the so-called cutting capacity.
|
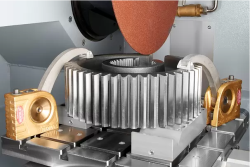 |
WET ABRASIVE CUT-OFF MACHINES
In metallographic sample preparation, mostly abrasive cut-off machines are used for sectioning of workpieces. Optimum cooling is just as important for the sectioning result as precise cut-off wheel guidance. Common cooling media consist of a mixture of a boric and amino acid-free corrosion protection agent with water. An appropriate concentrate is diluted with water in a ratio of e. g. 1:30. The manufacturer's instructions are applicable. Cleanliness (generally the top priority in metallographic sample preparation) must be ensured for the cutting chamber and drain system – this influences the cutting precision and the service life of the machine.
|
THE DIFFERENT CUTTING PROCEDURES IN METALLOGRAPHIC SECTIONING
|
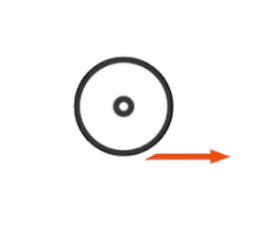 |
TRAVERSE CUT
Two versions are possible in this case:
- The sample table with the workpiece previously fixed on it is moved to the fixed cut-off wheel manually or automatically.
- The cut-off wheel is moved accordingly.
|
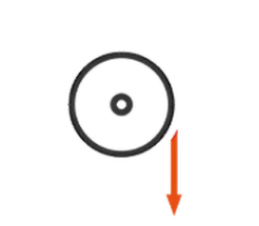 |
CHOP CUT
The workpiece to be cut is firmly fixed on the cutting table. The cut-off wheel is then manually or automatically guided from top to bottom into the fixed workpiece.
|
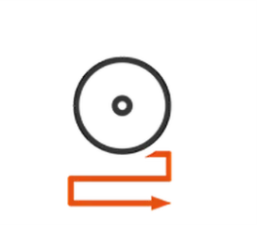 |
STEP CUT X
The workpiece is not cut in one cutting step, but in layers (stepwise). This type of cut is particularly suitable for cutting the large, thick workpieces of solid material.
|
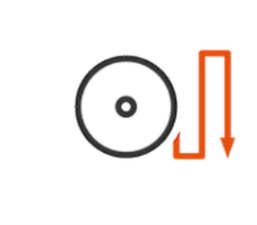 |
STEP CUT Y
The workpiece is not cut in one cutting step, but in layers (stepwise). This type of cut is particularly suitable for cutting the large, thick workpieces of solid material that must be clamped on edge (plates, angles, etc.).
|
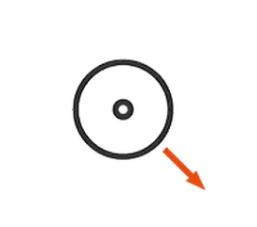 |
DIAGONAL CUT
In case of a diagonal cut, the table moves backwards (X axis) and the cut-off wheel moves downwards (Y axis) at the same time. This type of cut is particularly suitable for cutting asymmetrical workpieces, or for compensating the wear of the cut-off wheel in order to obtain a constant cutting depth.
|
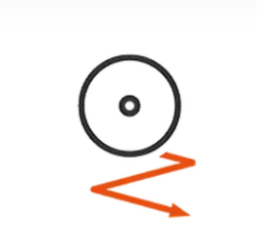 |
ZIG-ZAG CUT
The workpiece is not cut in one cutting step, but in layers (stepwise). The zig-zag cut is made in the middle of the component.
|
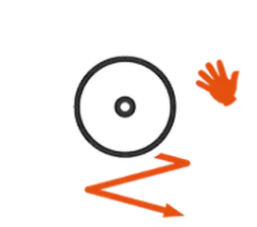 |
CARE CUT
During manual cutting, the clamping table (X axis) moves back and forth until the cut is completed. It starts with the movement from front to back. This type of cut is particularly suitable for workpieces where a clean cutting edge and material-friendly processing (temperature, deformation) is required due to the smallest possible contact surface.
|
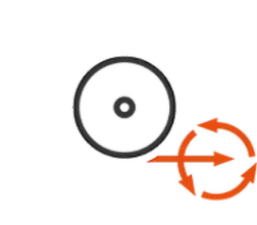 |
ROTATION CUT
This process is most often used on precision cut-off machines. It can also be used for large workpieces with corresponding rotary sample holders. The sample is turned clockwise or anti-clockwise towards the cut-off wheel. Quarter or half rotations are also possible. For a round workpiece with a diameter of 50 mm, only a cutting distance of 25 mm is required.
|
The contact area between sectioned workpiece and cut-off wheel should be as small as possible.
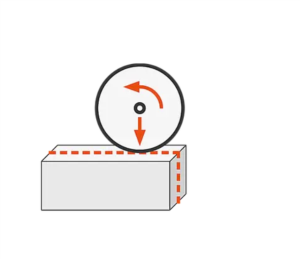
Large contact zone
|
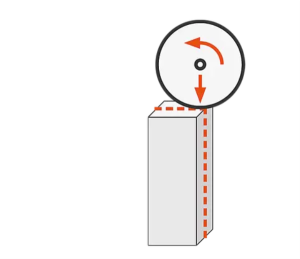
Small contact zone
|
|
HOW TO SELECT A SUITABLE CUT-OFF WHEEL
As a rule of thumb, the following principles apply for the choice of cut-off wheels:
- For hard materials, a cutting wheel with soft bond is recommended
- For medium-hard materials, a cutting wheel with medium-hard bond is best suited
- For soft materials, a cutting wheel with hard bond should be used
Most manufacturers specify either a manufacturing or best-before date. This must be observed since the binders of the bond are hygroscopic, i. e. they absorb water. Water in the bond can lead to embrittlement of the material after a few months or years. In this condition, the cut-off wheel is still usable, but with significantly higher wear and risk of breakage.For very ductile materials, such as titanium or plastics, cut-off wheels with silicon carbide as abrasive grain (also resin-bonded) are generally used.Diamond cut-off wheels are used for cutting very hard materials (ceramics, glass fiber reinforced plastics, minerals, glass, etc.). Here, two main bond-types exist: metal-bonded cut-off wheels, where the diamonds are usually embedded in a bronze bond, or those with a synthetic resin bond. The latter are particularly suitable for cutting very brittle materials.Cut-off wheels, in comparison to saw-blades, generate smoother and less deformed surfaces and breakouts on their entry and exit locations from the cut solid. This strongly reduces the thickness of the deformation layer, which has to be removed through metallographic grinding.
|
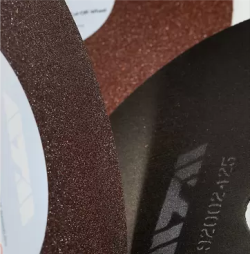 |
CUT-OFF WHEEL MATERIALS
Wear (i. e. abrasion resistance), service life and cutting performance are decisive for the quality of the cut-off wheel. Abrasive agents (aluminium oxide, silicon carbide, diamond, cubic boron nitride (CBN), etc.) and bonding (metal, synthetic resin or rubber) are characteristics of the wheel composition. The following tendencies can be taken into account for choosing a cut-off wheel for a specific cutting application:
- Corundum discs (aluminium oxide – Al2O3) with synthetic resin bond for all steels. Depending on hardness, optimized binders are used. This leads to a selection of cut-off-wheels suited for certain hardness ranges.
- Silicon carbide discs (SiC) for soft and medium-hard non-ferrous metals as well as hard non-metallic materials (glass, stone).
- Diamond cut-off wheels (C) for hard ceramic materials, ceramic composites and geological materials (rocks).
- Boron nitride wheels (CBN – Cubic Boron Nitride) for hard and tough Co- and Ni-based alloys, hard metals, hard composite materials, and hard to very hard carbon steels.
GRAIN SIZE OF THE ABRASIVES
The grain size of the abrasive in the cut-off wheel is an aspect that must not be neglected when cutting metallographic samples. It should be between 45 and 180 µm. This allows an optimally cut surface, which should facilitate further metallographic preparation without removal-oriented planar grinding, if all cutting parameters are set correctly. A very fine grain size is recommended when using thin cut-off wheels. A fine grain size is also important if burr-free cutting is required. The degree of hardness of a wet abrasive cut-off wheel does not say anything about the hardness of the abrasive grains, but rather about the hardness of the bond, i. e. about the resistance of the individual abrasive grain to breaking out of the bond material.
- A softer bond should be used for large-area contact points between the workpiece and the wet cut-off wheel. This also ensures that worn abrasive grains are broken out. This type of cut-off wheel is also well suited for heat-sensitive materials.
- In the case of smaller contact areas, a harder and more stable wet cutoff wheel is however suitable. Those are also used for cutting tubes and profiles. The advantage of this type of cut-off wheel is that it has less contact with the workpiece since the wall thickness is usually small.
TYPICAL ERRORS IN METALLOGRAPHIC CUTTING
The correctly selected cut-off wheel will produce edge shapes like:
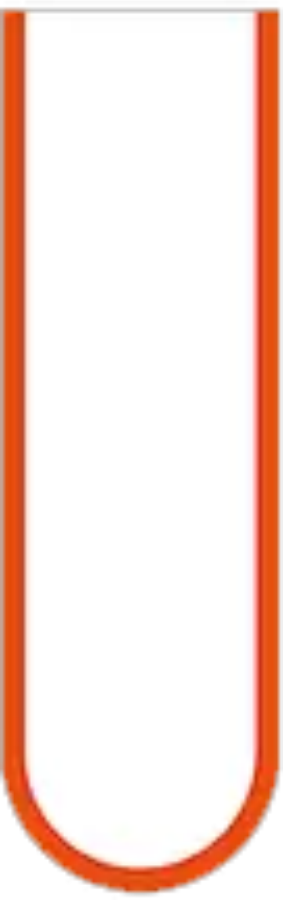 |
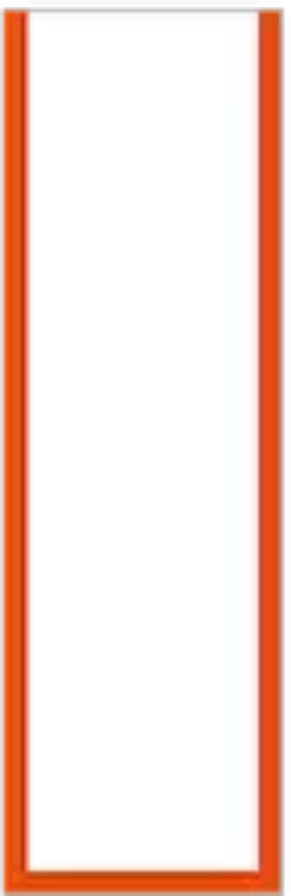 |
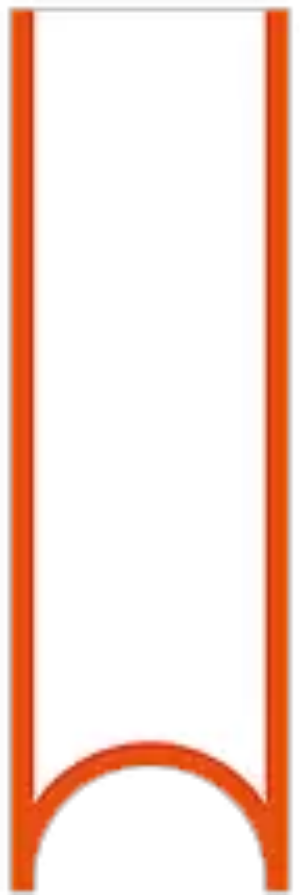 |
In case of solid material, rounded edges indicate the desired result. The correct cut-off wheel was used in the correct manner.
|
Sharp-edged corners are the sign of the correctly selected cut-off wheel for solid or profiled material as well as tubes of medium wall thickness.
|
Concave corners are the expected result when cutting thin tubes and cross-sections.
|
Incorrectly selected or applied, the wet cut-off wheel forms the following edge shapes: |
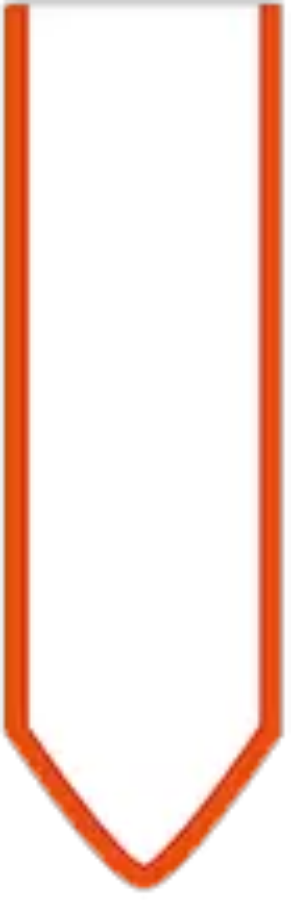 |
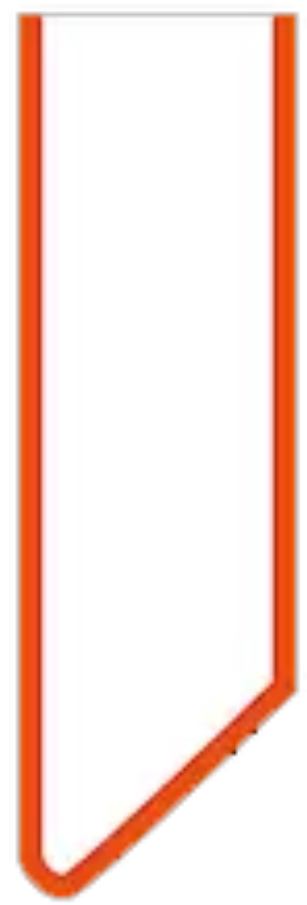 |
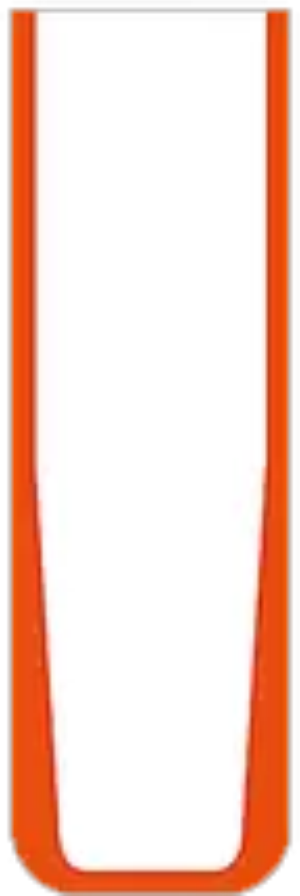 |
If the edges are sharp, an excessively hard cut-off wheel was used. The tapering effect can cause cut-off wheel breakage and burn marks.
|
Bevelled edges indicate incorrect or insufficient cooling. This can cause the cut-off wheel to lateral run-out and shorten its service life.
|
Glazed corners are formed if the abrasive grit is not broken out and the wheel may get clogged. In addition to an incorrectly selected wet cut-off wheel, excessively slow feed rate or insufficient rotational speed may also be the cause.
|
|
|
|